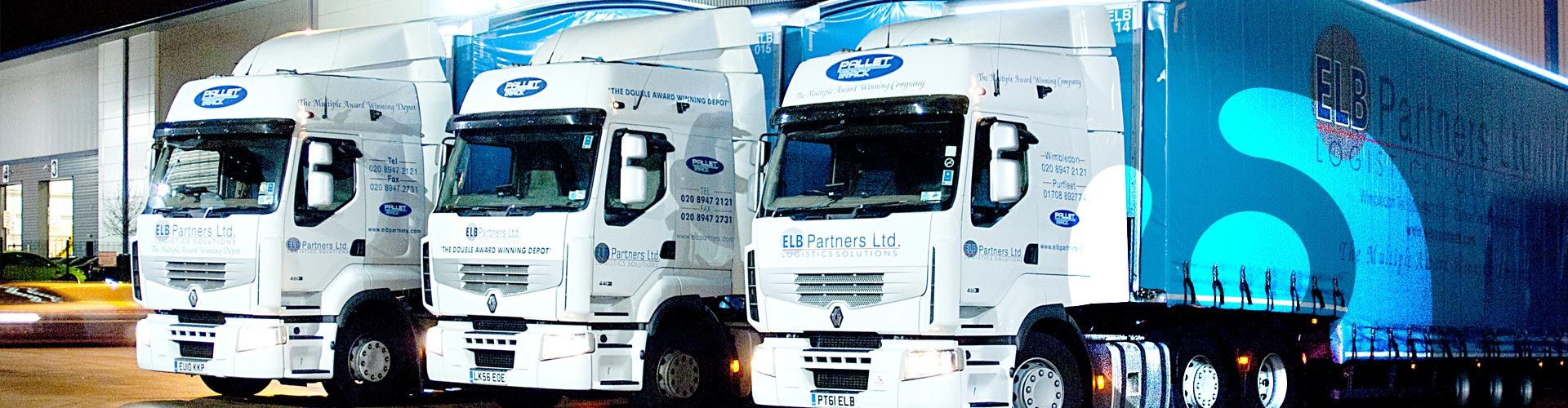
Pallet-Track Ltd
- Founded in 2002
- Grown from 46 to almost 90 members
- Transacts a daily average exceeding 14,000 pallets per night
“Having successfully partnered with Vigo Software for over fifteen years they were the obvious first point of call to help drive us into the future”
Customer profile
Pallet-Track comprises almost 90 haulier members who leverage the network to provide nationwide coverage to their customers. Established by Nigel Parkes, Managing Director, in 2002; Pallet-Track went live operationally in January 2004 with 46 members. In the first night of operation the network transacted 852 pallets through their Wednesbury Hub.
In October 2008 Pallet-Track relocated to a new 267,000 sq. ft. Central Hub in Wolverhampton, the Southern Hub commenced operations in 2014 and in August 2017 operations began at the Northern Hub, collectively Pallet-Track now transacts a daily average exceeding 14,000 pallets through its shareholder membership. The company is now well positioned to continue the excellent growth achieved to date.
Challenge
In today’s modern world it is vital to have an advanced, easily deployed and future proof IT solution. “Our IT infrastructure is the foundation of our Network” Carl Jones, Commercial Director at Pallet-Track comments. He adds “Automating manual procedures and eradicating duplication of tasks remains our ultimate objective”.
Having delivered a number of exciting and game changing technology solutions over the years Pallet-Track recognised the need to drive new innovation into the market place. Ensuring they continue to invest in the right technology to assist in the workplace, to provide accurate information and the tools to enable profitability and growth.
Solution
“We must continue to work smarter and simplify our technology in the future, providing system transparency, clear and concise statuses and improved planning tools” commented Carl Jones. “Having successfully partnered with Vigo Software for over fifteen years they were the obvious first point of call to help drive us into the future” he added. Together with Pallet-Track, Vigo Software designed and implemented a number of exciting technology solutions which include Central Billing, an automated process of inter-depot pricing via centrally generated purchase invoices and self bills; Electronic Customer Paperwork (E Doc), a fully automated customer paperwork solution; PlanIT, a superb next generation planning tool and Long Range Depot Scanning, a fast, effective and accurate scanning platform.
Carl Jones, Commercial Director at Pallet-Track said “We have designed and implemented a number of exciting technology solutions over the years and acknowledge in order to remain ahead of our competitors we must continue to revolutionise the market place.”
Darren Cronshaw, Owner Vigo Software added “We are working hard towards delivering great new products and are fully committed to Pallet-Track, its members and their customers”.
Results
The Central Billing system resulted in simplified financial administration and mutually agreed and resolved queries pre-invoice via the Price Amendment Requests on the Pallet-Track Web System. A single Purchase Invoice for costs and a Self-Bill for revenue are generated weekly by Pallet-Track itemising inter-depot activity for all consignments. This documentation is then distributed via email to all depots, creating a paperless accountancy process whilst improving productivity and reducing the associated costs for both the Hub and Depots.
Electronic Customer Paperwork process (E-Doc) is a fully automated, digital customer paperwork solution designed to remove the pressures associated with manual document sorting throughout the Network. Depots are able to scan the original paperwork or receive PDF’s via email which can be attached to the consignment. In all instances these documents transmit automatically via the software to the Hub system and the Delivery Depot. E-Doc has significantly improved productivity across the Network allowing members to share documents electronically
The ETA concept (PlanIT) is an essential component within the distribution sector to fulfil customer requirements. These planning tools will deliver ETA information throughout the network along with superior vehicle utilisation and cost visibility, providing accurate information and improved customer service.
Enhanced planning tools along with a fantastic ETA solution will provide the entire network significant benefits, including cost analysis tools, simplified job allocation and a view of live statuses, all of which improve inter depot and customer service standards. Gross margin reporting, superior mapping capability and single route optimisation will aid vehicle utilisation helping to reduce costs. Making use of these tools is essential to help improve profitability. The objective is to provide customers with an accurate ETA solution unparalleled in our sector.
This new depot scanning solution is available on both Intermec and Motorola hardware and provides long range capability, increased functionality and a modern touch-screen interface.
Enhancements to the discrepancy process includes photo capture capability and simplified yet detailed submission of pallet dimensions. These improvements have refined and completely revolutionised the discrepancy process throughout the network.